A Modal Survey Test of "Kibo" conducted |
| 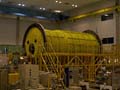 |
PM Qualification Model |
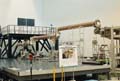 |
Engineering Model of the Manipulator |
A Modal Survey Test was conducted on the Pressurized Module (PM) and the
Manipulator of "Kibo", the Japanese Experiment Module (Kibo),
at Tsukuba Space Center from May 28 to June 4, 1999.
 | What
is a Modal Survey Test? | A Modal Survey Test is conducted
to determine the vibration frequency at which the object tested begins to resonate.
 | Test
Objective | Kibo will be launched by three Space Shuttle flights.
During a launch, the Shuttle vibrates vigorously, which causes Kibo to vibrate
in the same manner. Kibo's vibration is fed back to the Shuttle. If this vibration
is large, it could affect the attitude of the Shuttle. To avoid excessive
vibration, all cargo in the Shuttle payloadbay is assigned a range of safe vibration.
Using computer simulation to analyze a mathematical vibration model of each piece
of cargo, NASA confirms that cargo vibration will not affect the Shuttle launch
safety. The PM and the Manipulator are combined in a launch configuration
and subjected to vibration to obtain vibration data. The data is compared with
the data simulated by the vibration model that was set up during the design phase
of Kibo. The Modal Test is conducted to confirm that any differences between the
two sets of data stay within an acceptable range.
 | Test
Method | The test was conducted using the Qualification Model
of the PM and the Engineering Model of the Manipulator. The PM with the
attached Manipulator is first installed on the simulated support structure, which
fixes the cargo in the payloadbay of the Shuttle. Data is then collected from
over 400 acceleration sensors, attached to the PM and the Manipulator while applying
vibration from zero to 100 Hz randomly, with a force of 15kgrms. Also, a simulation
of this test is performed using the vibration model that was set up during the
design phase of Kibo. The results of this simulation and the data obtained by
this Modal Test are compared. If the differences between them exceed the predetermined
limits, the vibration model will have to be modified so that the differences fall
in the acceptable range. It will take about half a year to evaluate the test results
and modify the model. The completed vibration model will be submitted to NASA.
NASA will apply this model in the Shuttle and payload launch configuration vibration
tests and confirm the launch safety. 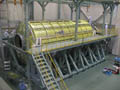 | 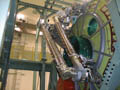 | 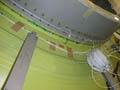 |  |
Feature of the
test configuration | Manipulator
(front) and PM (back). | Acceleration
sensor | Vibrator |
 | Comments
from NASDA' s key person | 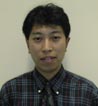
Kaoru Miyake JEM project Team Space Environment
Utilization System Department National Space Development Agency of Japan
| |
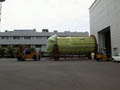

From the Space Station Test Facility to the Spacecraft
Integration and Test Building. | Securing the test area
was the toughest thing I had to do. At Tsukuba Space Center, Kibo is not the only
item being developed. Satellites are being developed and tested, and other technology
developments are under way. Negotiations with other sections to secure the test
area are the major activities. When the test area is finally acquired, it is time
to start test preparations. Experiment racks will be installed inside PM. The
racks are simulated by dummy racks which simulate the weights and centers of gravity
for the launch configuration. Transporting Kibo, which weighs a total
of 15 tons, is the next problem. It takes about four hours pulling by a forklift
truck to move it from the Space Station Test Facility to the Spacecraft Integration
and Test Building, several hundred meters away. From the entrance of the Spacecraft
Integration and Test Building to the test area, we move Kibo manually using ten
people. We next set it on Air-skates, which expel compressed air to float their
loads on the floor, then we push. After six hours of effort and plenty of sweat,
Kibo reaches the destination, where we can finally start the test.
|  | Procedure
for moving Kibo's PM inside the test facility | The 15
ton PM is moved as shown below. 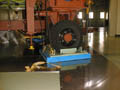
| 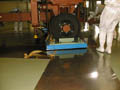
| | 1. | Kibo
is put on plates called Air-skates, that expel compressed air to float the load.
The blue plate is the Air-skate. Two Air-skates are installed at the front and
back of Kibo respectively. | 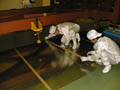
| | 2. | If
air leaks from the junctions of floor tiles, Kibo does not float. To avoid this,
we construct a path by placing aluminum plates on the floor covering the plate
junctions with adhesive tape. | 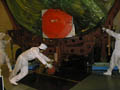
| | 3. | Compressed
air is expelled to float Kibo so it can be moved by hand. | 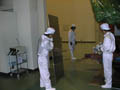
| | 4. | When
Kibo reaches the end of the aluminum path, we move the aluminum plate forward
and repeat this until Kibo reaches its destination. | 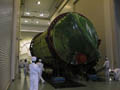 | 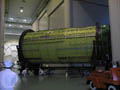 | | 5. | After
30 minutes of effort, we could move this much. In spite of the air conditioning,
working in clean room overalls causes heavy sweat. |
Last Updated : August.6, 1999
|