Interviewing a key person at "Kibo" (Japanese Experiment
Module) manufacturing site. |
|
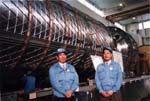 |
Left Mr. Fukuda, right Mr. Yamaguchi. |
On March 1, 1999, a sunny day which reminded me of early spring arrival,
I visited the Asuka factory of Mitsubishi Heavy Industry (MHI) in Nagoya, where
JEM's PM, and ELM-PS are being assembled. In the factory, JEM PM's aluminum
alloy outer shell structure with many triangular cut-out patterns were almost
completed, and internal assembly was progressing with launch targeted in 2004.
This is an interview report with MHI's Mr. Fukuda who is responsible for
this project, and Mr. Yamaguchi who is responsible for equipment design.
Q1: | What
is MHI's position in this project? | MHI: | In
this factory, we manufacture structural part of JEM's PM and ELM-PS. We also integrate
parts which other manufacturers developed and items purchased from overseas. Integration
combines parts and assures the completeness of the total system. During preparation
activities, we checked out the parts in various ways. We used to find many new
problems in the integration, since many of the parts are newly developed. The
interfaces between Space Station modules are common throughout the International
Space Station. U.S. (Boeing co.
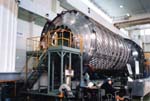 | 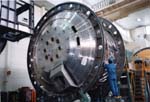 |
MHI is responsible for flight
models of both the Pressurized Module (left), and ELM-PS (right). |
ltd.) produces the interface part. If its design is changed by the US,
JEM's design also has to be changed. This affects our task schedules, and we face
difficulties in international technical negotiation. |
Q2: | MHI produces aircraft and
rockets. How do they differ from JEM? | MHI: |
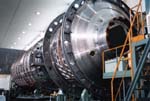 |
Producing JEM requires high level technology. |
Rocket missions are short, so there is no need to maintain them after
they are launched. Aircraft can receive maintenance after the flight, on the ground.
After Space Station is launched, however, only astronauts are available, so it
has to be designed considering maintenance and operations activities performed
by astronauts only. Also, if a space suit is damaged during extravehicular activities,
it is very dangerous, so it is very important to design the equipment with no
sharp edges. To avoid air leaks, primary structure is produced by welding a large
aluminum sheet. Welding an aluminum structure that is four meters in diameter
requires extremely high-level technology, which MHI is proud of. Welded parts
are checked by X-ray testing. | Q3: | What
is the most difficult point? | MHI: |
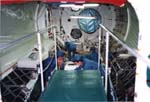 |
Inside pressurized module under assembly |
We conduct various tests at various production stages. Since the Space
Station is a very new project for Japan, and requires new concepts in designing
and manufacturing, it is not easy to anticipate problems. Many unexpected problems
annoy us after tests have started, so schedule management is very difficult. Troubles
in space are unacceptable. We conduct special management and inspections by applying
a procedure called a Fracture Control. We realized that special attention should
be paid to propagation of mildew and bacteria in the cabin. To prevent such propagation,
we install heaters on the outer shell structure to prevent water from condensing
on the cabin walls. We also adopt paints which resist propagation of mildew or
bacteria. | NASDA: | Thank
you for shearing us your busy time. |
Last Updated : August.6, 1999
|