Functional Test of the airlock of Japanese Experiment Module
"Kibo" |
| A functional test of the airlock
of Japanese Experiment Module "Kibo" was conducted inside the flight
model of Kibo's Pressurized Module (PM) on August 4 and 5, 1999. Here is the report.
(For detail of an airlock see Kibo Structure
-Airlock-. )  | What
is an Airlock Functional Test? |
Kibo's airlock is a gateway through which experiment equipment
and other items will be transferred between Kibo's Pressurized Module (PM) and
the Exposed Facility (EF) which is located in space vacuum. The airlock has two
hatches, an inner hatch inside the PM and an outer hatch outside the PM. (See
the figures below.) Neither hatch can be opened unless the other one is closed.
In order to prevent precious air from escaping to space, the air inside the airlock
is recovered into the PM before the outer hatch is opened to transfer the objects.
The test was conducted to confirm that both hatches and the slide table can function
as designed. | 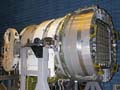
Airlock | 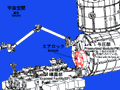 | 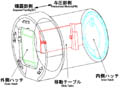 | 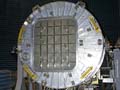 | 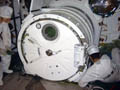 |
Airlock location & structure | Outer
Hatch | Inner Hatch |
 | Test
Scenes | |  | Hatch
Functional Tests | | - | | The
outer hatch can be opened and closed electrically, but the inner hatch is operated
by hand. There are two ways to operate the outer hatch electrically, auto mode
and manual mode. The auto mode performs the hatch opening and closing procedures
automatically when a crew member pushes a button. The manual mode is executed
by a crew member confirming each individual step by pushing a button. Also, the
outer hatch is designed to be operated by hand when electric power is not available.
This test confirmed that the hatches can be opened and closed in both modes as
designed. | 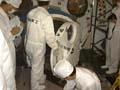
Test Scene | | | The
test scenes below are available. |
- |  | Slide
Table Functional Test | | |
| | The slide table is used to
move Orbital Replacement Units (ORUs) and experiment equipment to and from the
PM and EF. It is located inside the airlock. It secures an ORU by latches on both
sides of the table, fixes it in position, then moves. Like the outer hatch, this
slide table can be moved electrically (in both auto mode and manual mode). It
can also be operated by hand when electric power is not available. This test confirmed
that the slide table functions fine in both operational modes. | 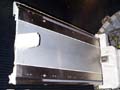
Slide Table | 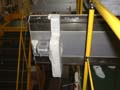
An ORU being secured | | | The
test scenes below are available. |
|  | Other
Tests | | - | | The
inner hatch is operated by hand. The force necessary to open or close the inner
hatch was measured. A seal on the edge of the hatch prevents air leakage from
the gap between the hatch and the airlock wall. When the inner hatch is closed,
the seal fills the gap. Some seal deformation is necessary for the seal to function
normally. The gap was measured to confirm that an appropriate volume for seal
deformation is available. | 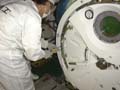
Measuring the force needed to open the hatch by hand. |
 | Tests
to follow | Following this test, a pressurizing and depressurizing
equipment test and a leakage test will be conducted. When ORUs are moved between
the PM and space, the airlock will be depressurized to recover the air. Equipment
for this purpose will be tested in the pressurizing and depressurizing equipment
test. A leakage test will also be conducted to confirm that no air leaks from
the ducts and hatches. The above two tests will complete the series of
tests conducted for the airlock only. After these two tests are finished, integrated
tests will be conducted in conjunction with other Kibo subsystems.
Last Update:Sep. 29, 1999
|